More Efficient Copper Catalysts
A team of researchers from the Department of Interfacial Sciences has discovered how changes in the structure of copper catalyst particles during electrochemical CO2 reduction affect their catalytic performance. This should lead to the development of new catalysts that convert the greenhouse gas CO2 into useful chemicals.
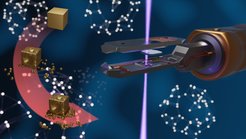
Using electrocatalysis to turn simple molecules commonly found in our environment into useful chemicals and fuels is an important strategy for storing energy from renewable sources effectively and enabling a circular economy. The electrochemical reduction of CO2 (CO2RR) is a key aspect of this approach, where CO2 molecules are recycled back into hydrocarbons for later use – analogous to how plants convert CO2 into carbohydrates and sugars with photosynthesis – while at the same time, mitigating the impact of CO2 emissions. Here, a selective and stable catalyst is critical for economic viability. However, it is not an easy task to find such catalysts because of the complex relationship between the catalyst structure and performance. Moreover, the catalysts can change their characteristics depending on their environment and we know very little about these changes because of the challenges faced when trying to observe how catalysts evolve during reaction.
A team of researchers from the Interface Science Department of the Fritz Haber Institute of the Max Planck Society have now managed to record movies of these structural changes. “In situ transmission electron microscopy is the premier technique for capturing fine-scale electrocatalyst dynamics and we were able to record high quality movies of these nanoscopic changes,” explains Prof. Beatriz Roldán Cuenya, the Head of the Interface Science Department. “The big challenge is how to associate what’s happening in the microscope with its impact on catalyst performance, which is measured in laboratory scale reactors.” Here, parallel efforts between the electron microscopy and the electrochemistry groups looking at identical catalyst particles finally solved this conundrum.
The researchers had to first devise a way to make the exact same catalysts in different setups. “Electrodeposition turned out to be the most elegant approach by which we can tune the size, shape and spatial density of catalyst particles,” says Dr. See Wee Chee, Group Leader at the Interface Science Department. “Then, by matching the behaviour of specific catalysts with their performance, we are able to determine the impact of these structural changes on their product selectivity during CO2RR. In particular, we are able to show that the catalysts change very early in the reaction process especially the smaller ones, which exhibit changes as soon as they are immersed in the electrolyte”.
The team found that two processes affect the actual number of catalysts during reaction. First, some of the catalysts dissolve or drop off as soon as the particles are immersed in the liquid electrolyte. Second, some of the material lost can be recovered in the form of new re-deposited particles once a potential is applied. These two effects can drastically alter the actual number of catalysts and impact their performance. If catalyst loss dominates, the resulting performance is poor. More importantly, the experiments show that larger cubes are also more stable, and we can achieve selective and stable performance by starting with a high density of such cubes. In this case, the empty space between cubes is further filled up by the re-deposited particles, which facilitates the formation of hydrocarbons.
“These studies show how the starting number of catalysts particles, their size and density on the support electrode surface is not a reliable indicator of the actual number of particles present during reaction.” explains Dr. Philipp Grosse, one of the lead authors on the paper. “More importantly, we show that by optimizing the design of the pre-catalyst structures, we can also influence their structural evolution under working conditions and thus also their selectivity.” “It is also very exciting for the electron microscopists”, adds Dr. Aram Yoon, another one of the lead authors, “This is a clear demonstration that we can perform systematic and reproducible electrochemical experiments in the microscope.”
These studies are expected to change how we view the impact that catalyst restructuring under reaction conditions has on the catalyst performance. Furthermore, the lessons learnt from looking at how the copper catalyst evolution varies as a function of the starting morphological parameters of the pre-catalyst can also inspire new ideas about how to design active, selective and stable catalysts with optimal working conditions. Moving forward, the Liquid Electron Microscopy group led by Dr. See Wee Chee aims to use similar ideas to gain in-depth insight into structure-property correlations in electrocatalysts in other technologically important reactions for sustainable energy such as water splitting (a reaction in which water is broken down into oxygen and hydrogen) for green hydrogen production and nitrate reduction (a promising reaction for electrochemical ammonia production and pollution mitigation).